You have choices, make the right choice

Model to Measurement: Automating Inspection from CAD to Real-Time Quality Control
Mitutoyo Integrated digital inspection ecosystems eliminate manual programming, accelerate reporting, and empower teams to act on live data before parts drift out of specification.
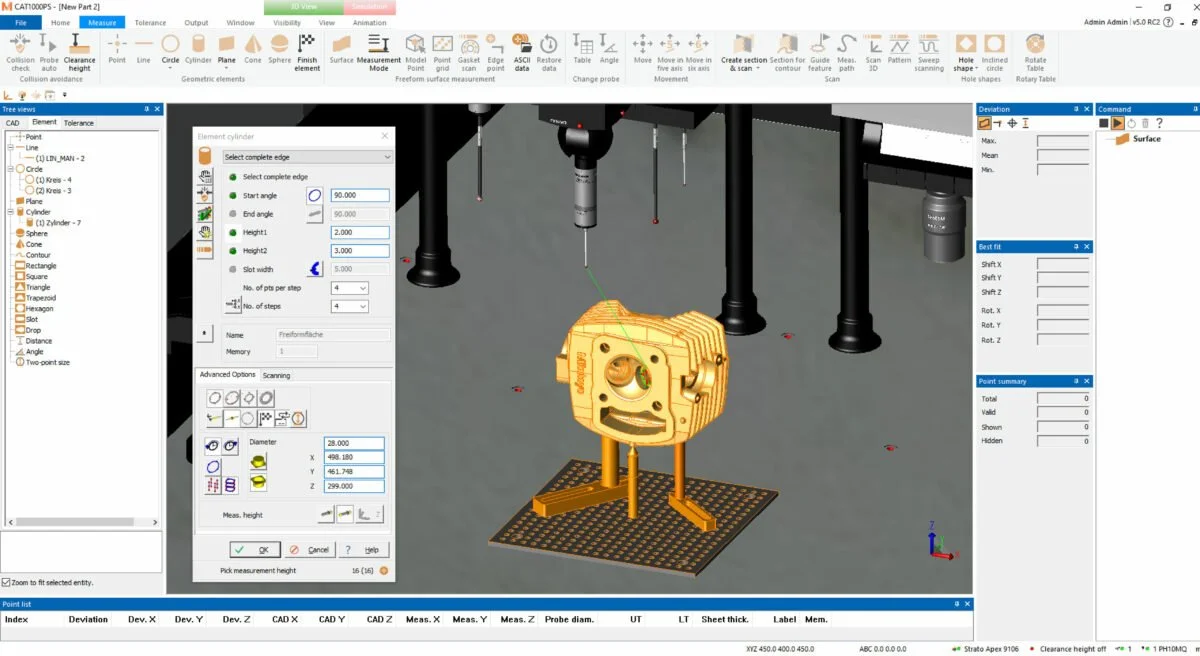
Mitutoyo MCOSMOS: Harnessing CAD-Driven Metrology
Mitutoyo’s MCOSMOS is the industry-leading metrology software suite that transforms a coordinate measuring machine into a fully integrated, CAD-driven inspection environment. At its heart lies PartManager, the command center that organizes all measurement tasks, data, and reports.
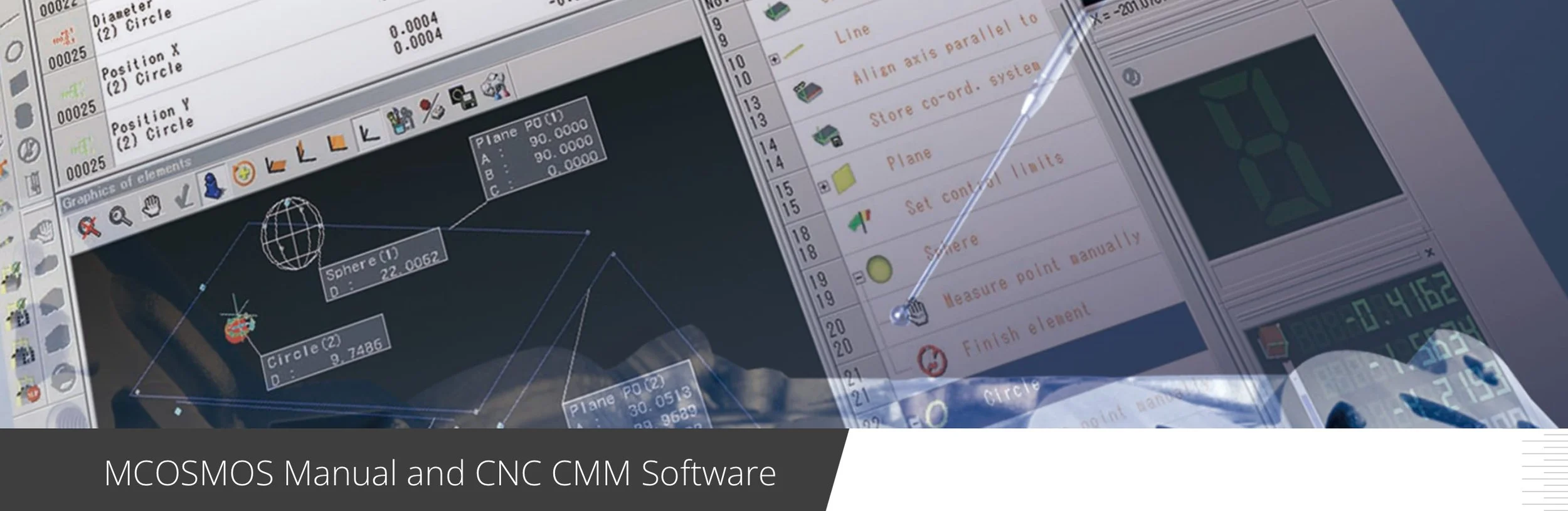
Mitutoyo America Corporation Releases MCOSMOS V5.4 Advanced Metrology Software Suite for Coordinate Measuring Machines to Improve Measurement Efficiency
Mitutoyo America Corporation, the leader in metrology instruments, solutions and support, announces the release of MCOSMOS V5.4, the latest version of advanced metrology software suite for coordinate measuring machines (CMMs). This update improves CMM operability with faster setup, reduced downtime, improved measurement throughput giving you the competitive advantage in digital manufacturing.
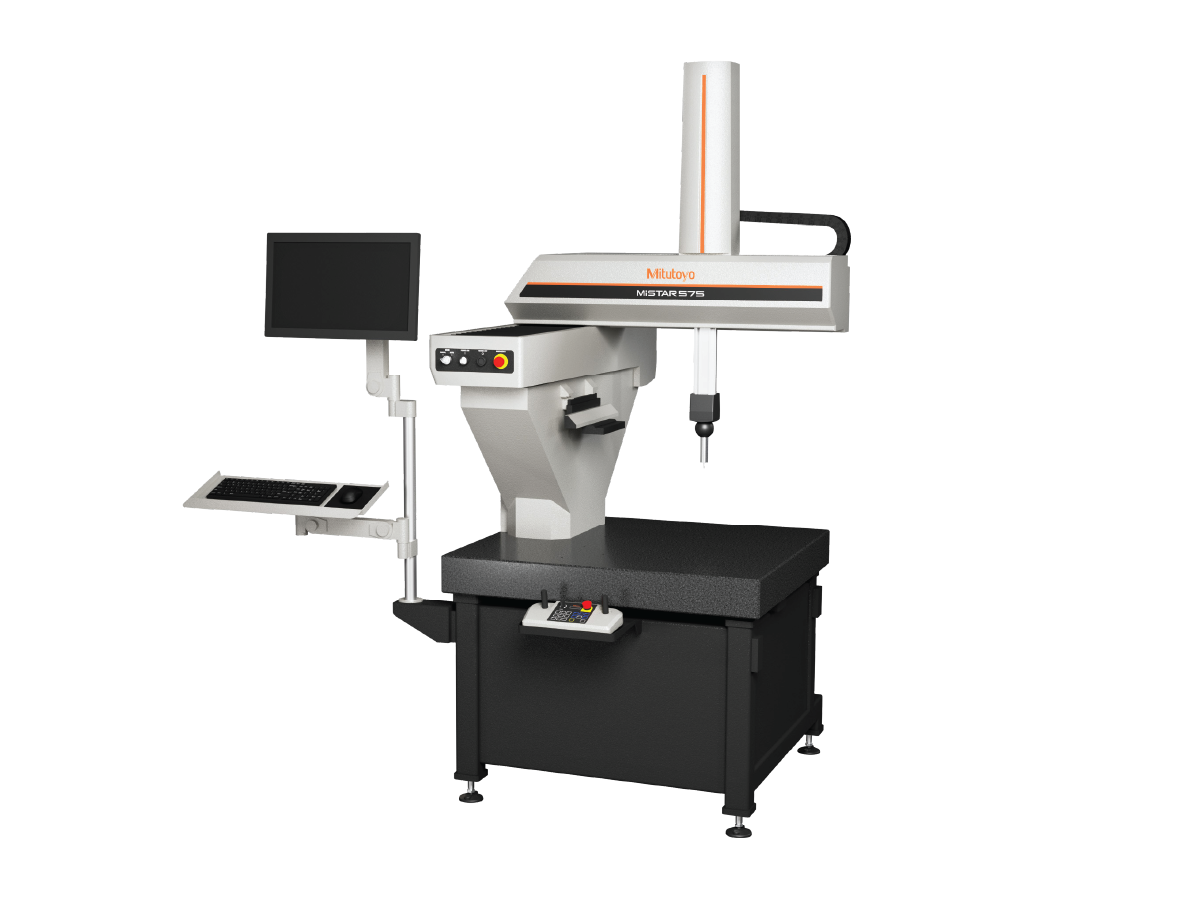
Invest in Precision: Mitutoyo America Corporation Announces Limited-Time Savings on MiSTAR 555 and 575 Coordinate Measuring Machines
In today's unpredictable economy, one investment still delivers lasting certainty: Precision is the smartest investment. For a limited time, Mitutoyo America Corporation, the trusted leader in advanced metrology solutions, is offering a rare opportunity to invest in the future success of your inspection capabilities with exclusive promotional pricing of up to 26 percent off the MiSTAR 555 and 575 CMM through September 30, 2025.
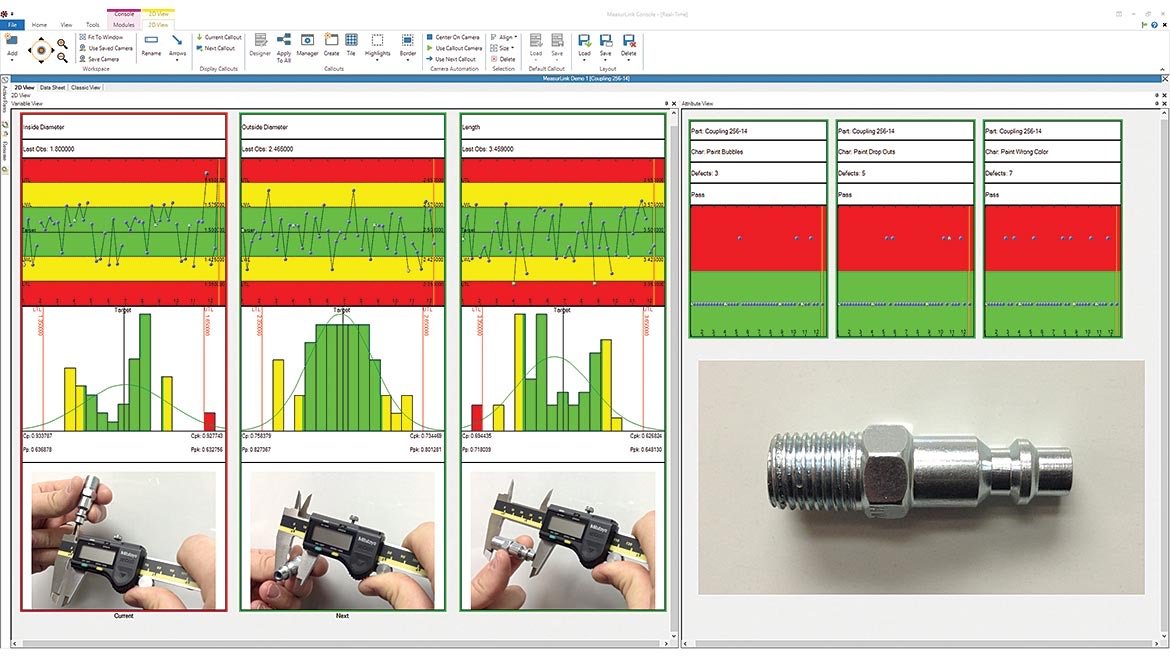
Beyond the Measurement: How Data Management Software Can Transform Modern Manufacturing
When it comes to measurement data software, it’s easy to think the discussion begins and ends with raw measurement values, but it’s about much more than that. Yet many shops still see “quality data” as nothing more than a list of measurement values. In this article, we will discuss and highlight the many benefits of deploying a higher quality of measurement data software throughout your manufacturing company and show how measurement data software delivers much more than numbers.
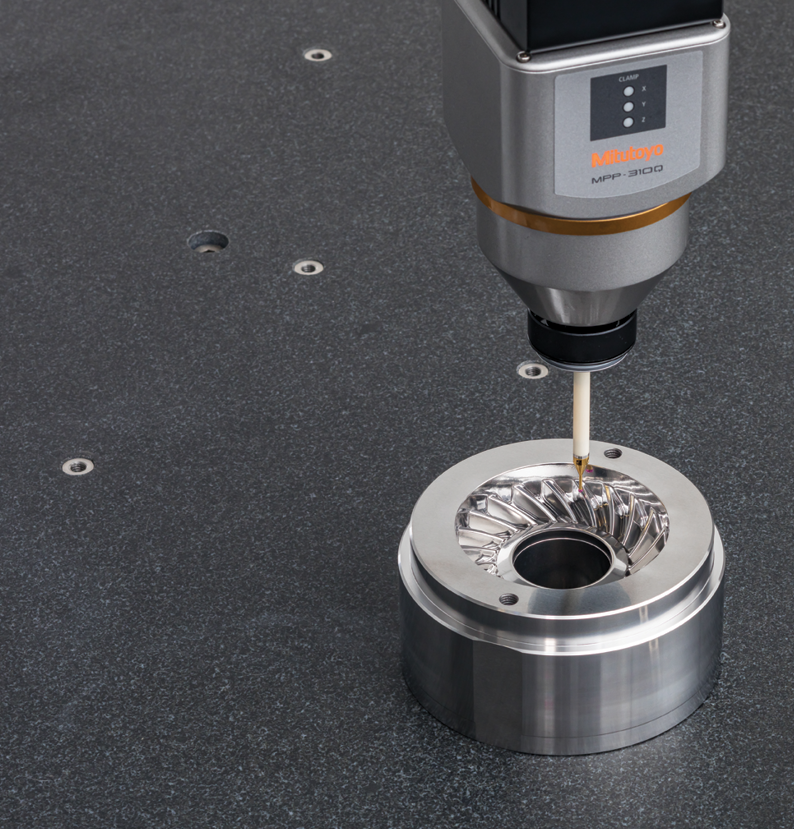
Coordinate measuring machines hit the target for weapons standards
In weapons systems manufacturing, one imprecise part can compromise an entire system – and an entire mission. That’s why there are no standards quite like defense standards, and why weapons system manufacturers must ensure precise parts measurement, particularly in barrels, firing mechanisms, and triggers.

Digital Twins: Elevating Manufacturing Standards and Reducing Errors
Digital twins, once a concept reserved for speculative fiction, now stand at the forefront of modern manufacturing and quality control. These virtual replicas of physical assets that range from individual machines to entire production lines, enable organizations to simulate, test, and optimize processes before making real-world changes.
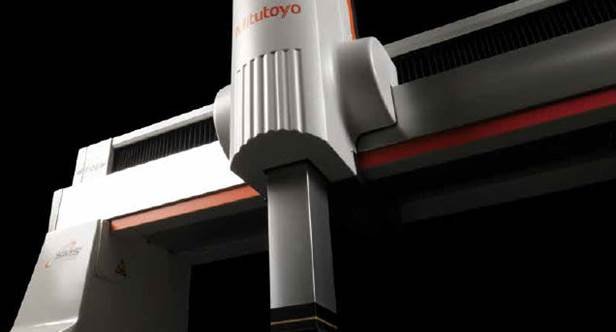
Why 3D Comparative Gages Fall Short in Quality Inspections Compared to Modern CMMs
In modern manufacturing environments, precision and efficiency are critical—not only during production but also in the inspection process. To maintain high standards of quality and compliance, manufacturers increasingly rely on automated measurement systems.

Shop Floor CNC CMM Delivers Next-Level Accuracy and Performance for Larger Parts
Mitutoyo America Corporation has announced the launch of the MiSTAR 575 Shop Floor CNC Coordinate Measuring Machine (CMM). Building upon the success of MiSTAR 555, the MiSTAR 575 takes shop-floor performance, accuracy, and measuring range to new heights, offering unparalleled capabilities for a wide range of applications.

Coordinate measurement simply different Racing skis to the test bench
Their passion for the project is easy to see in Mario Lazzeri and Johannes Brunner, because the two Austrian students have devised a more than exotic theme for their student research project.
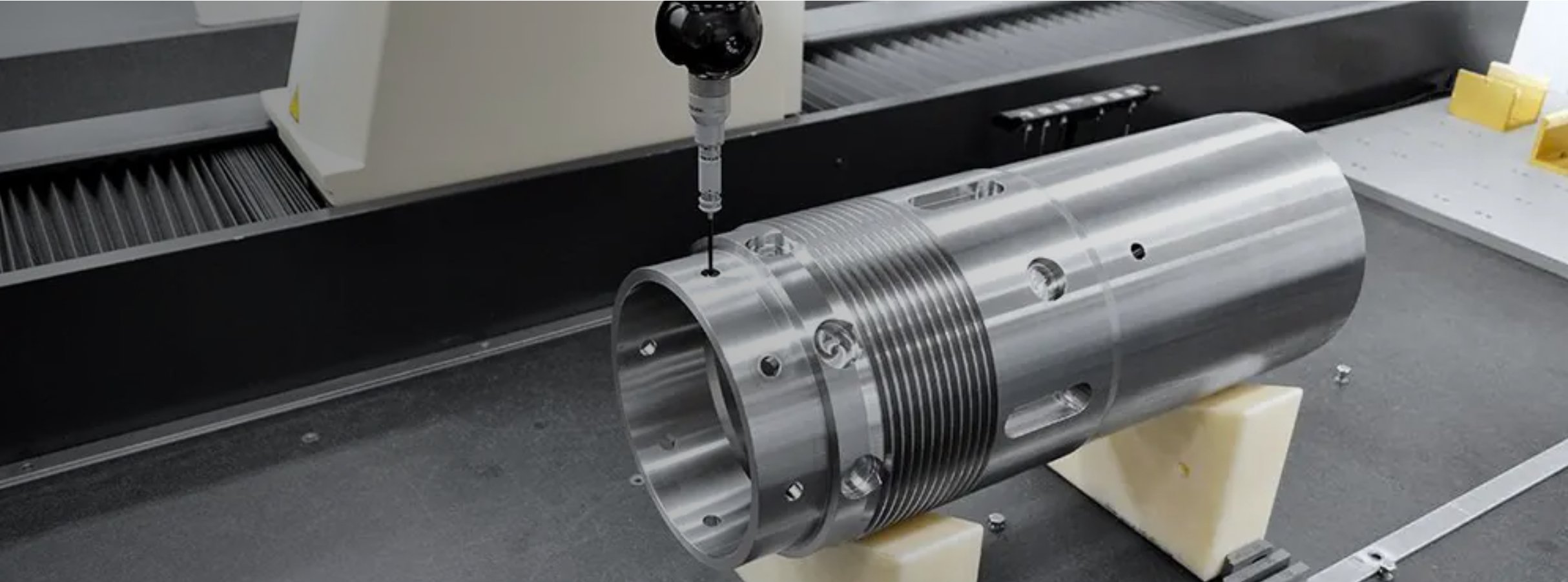
LPE ‘Coordinating’ Quality with Mitutoyo
The quality, reliability and longevity of manufactured products is continuously improving, in addition to enhanced design techniques and developments in material science, this progress is largely due to the use of advanced quality control methods and equipment and the application of tighter dimensional tolerances.
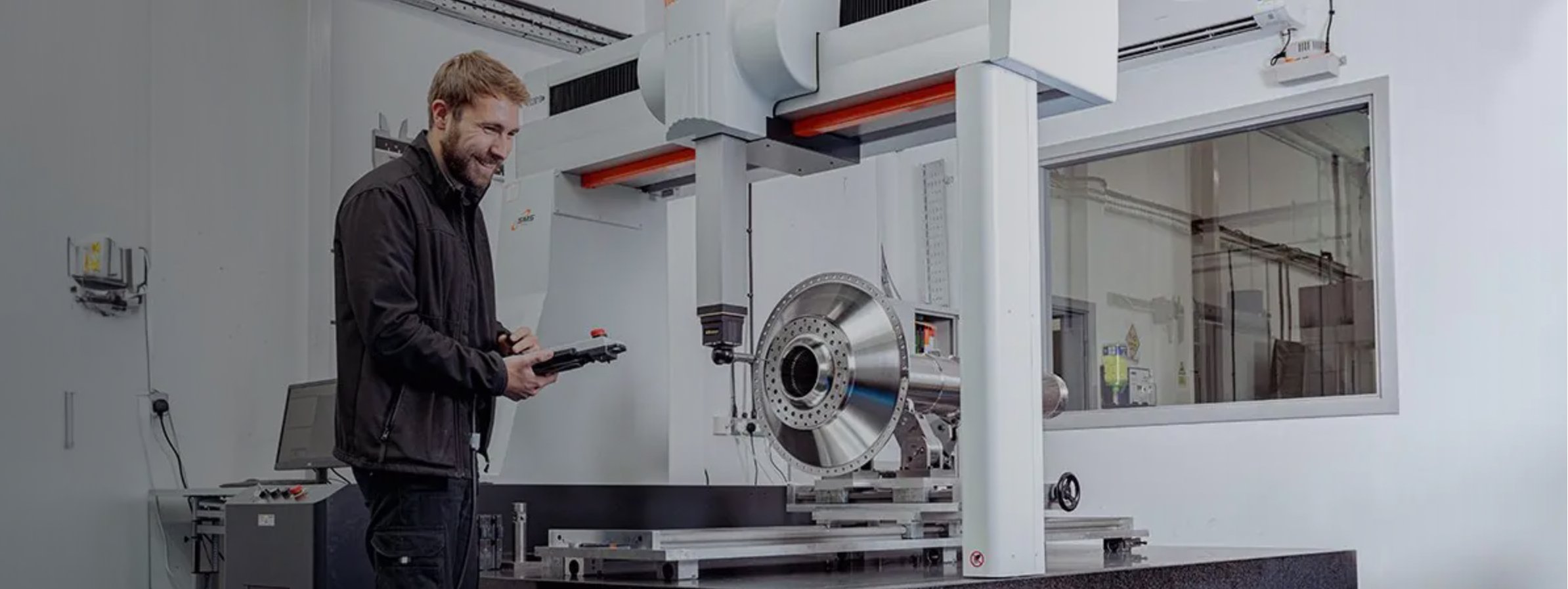
Mitutoyo CMM Ticks all the Boxes for AML
Just as manufacturers look to achieve increased production efficiencies and improved quality levels by investing in the best available machine tools, farsighted businesses are increasingly applying the same criteria to their Coordinate Measuring Machine (CMM) purchases.
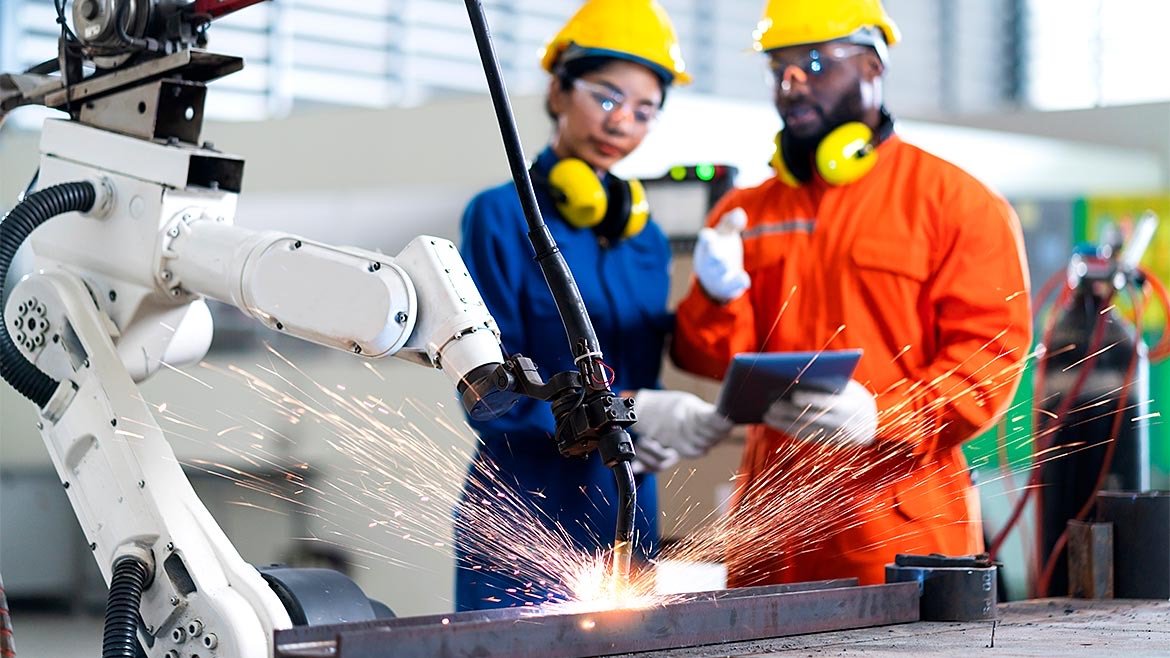
The Revolution of Automation and Metrology in Modern Manufacturing
Modern manufacturing demands the production of components with tolerances that push the boundaries of conventional measurement methods.
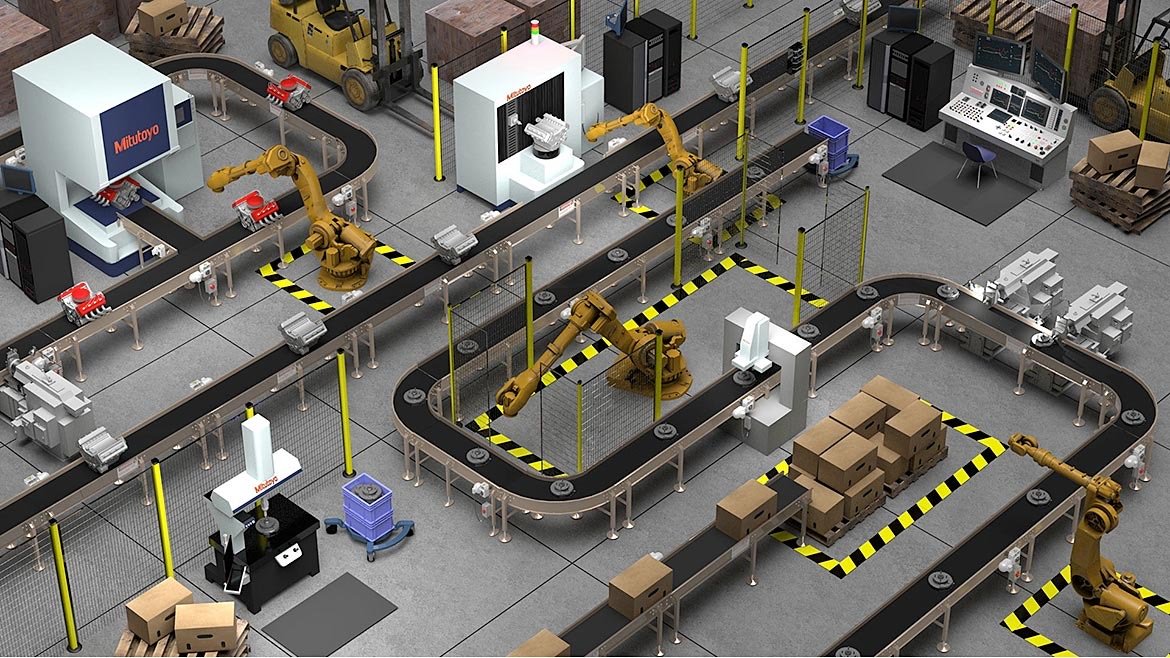
The Rise of Industry 4.0 and its Impact on Metrology
As smart factories have grown to embrace more advanced technologies such as AI, machine learning, and smart sensors, they’ve also evolved to include more developed forms of metrology.
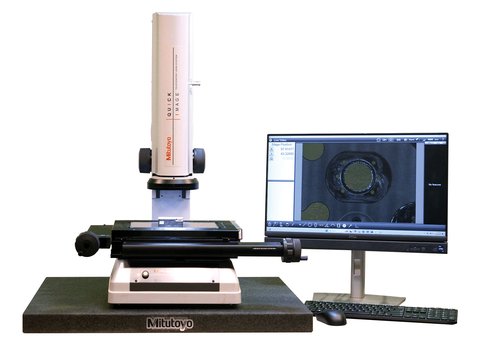
Mitutoyo America Corporation Releases New Metlogix M3 with the Mitutoyo Quick Image Vision System
Mitutoyo America Corporation, a leader in precision measuring instruments, is excited to announce the integration of the powerful Metlogix M3 software into the Mitutoyo Quick Image (QI) 2D Vision Measuring System. This latest enhancement promises to elevate the precision and efficiency of non-contact measurements, further solidifying Mitutoyo’s commitment to providing innovative technology solutions to meet modern quality control needs.
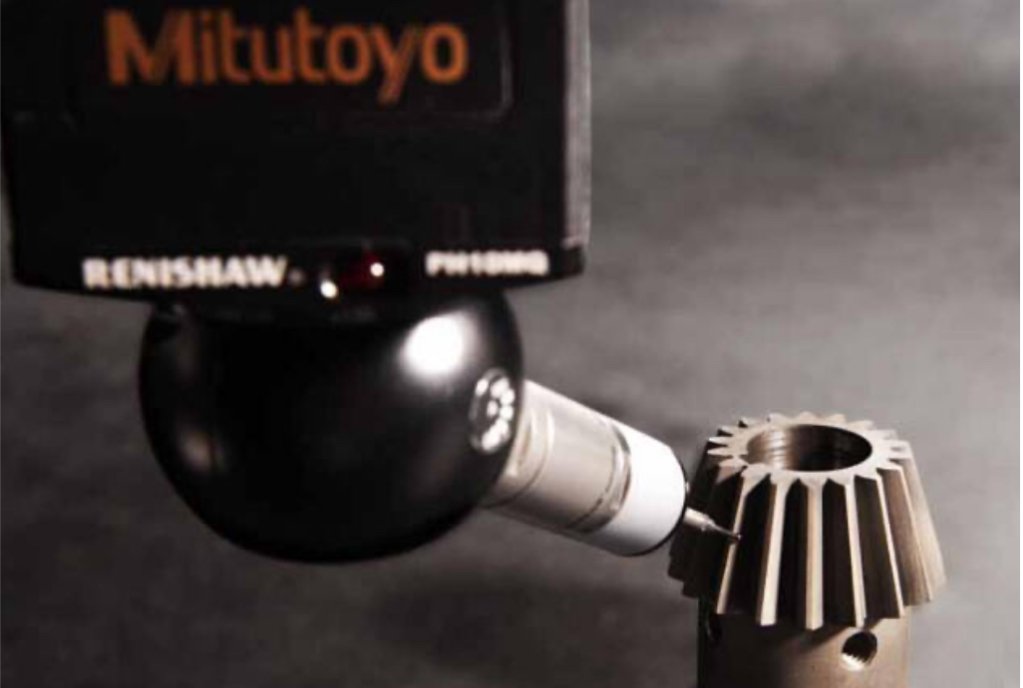
CONSIDER A CMM FOR GEAR INSPECTION
Gear inspection has long been considered a highly specialized, expensive and difficult part of the gear manufacturing process, requiring a wide variety of complicated gages, testers, dedicated CNC equipment and highly trained experts.
But if you want to make good gears, you need to have all that stuff, right?
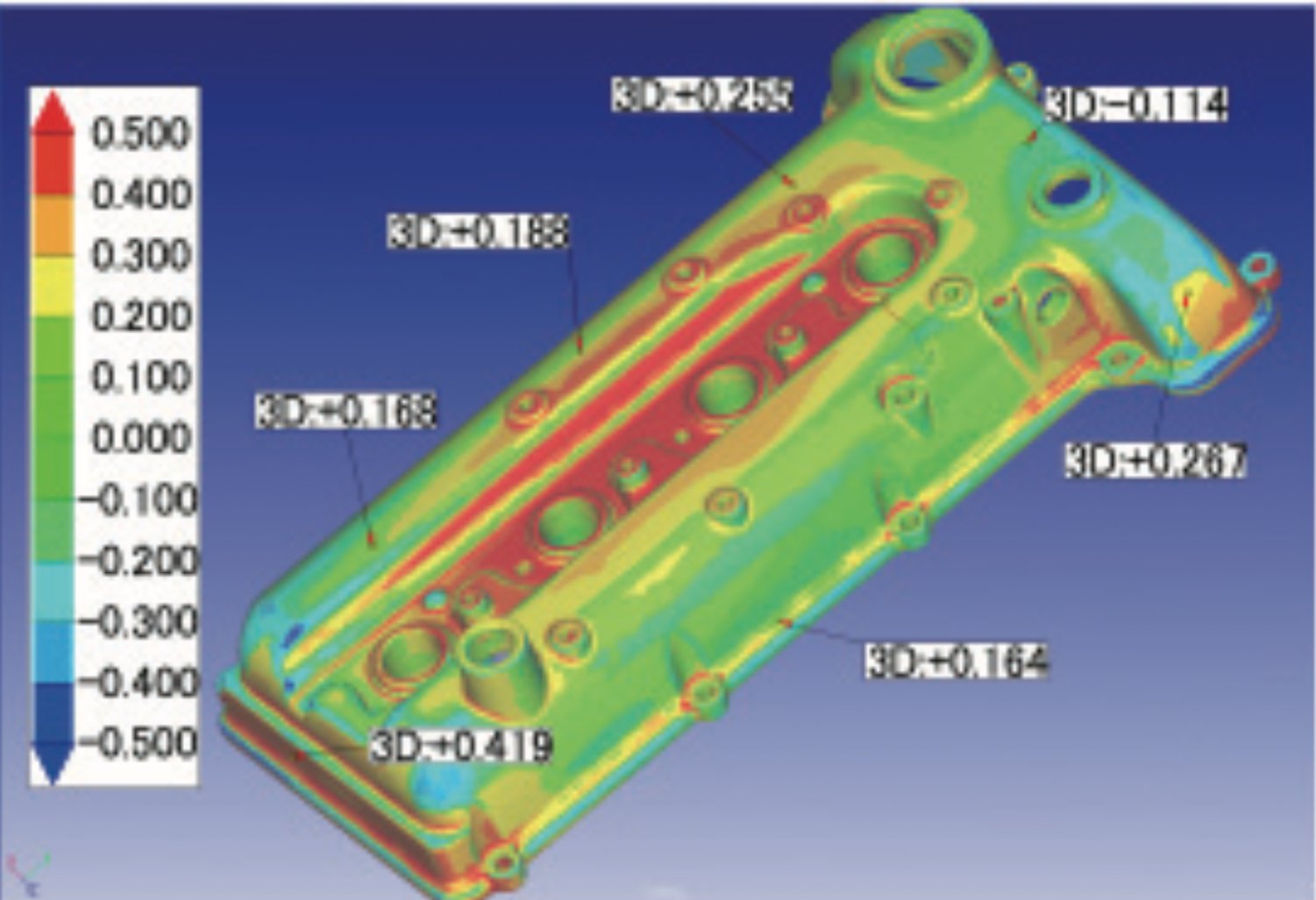
EXPAND YOUR CMM’S CAPABILITIES
During the past 25 years, coordinate measuring machine (CMM) sensor technology has expanded from tactile and scanning systems to now include optical, laser and surface finish sensors, effectively expanding the CMM’s capabilities. While each CMM sensor technology has its own advantages and limitations, the expanded measuring capability provided to the CMM compels anyone with measuring requirements to consider adding additional sensor technology to a current CMM or for a new CMM purchase.
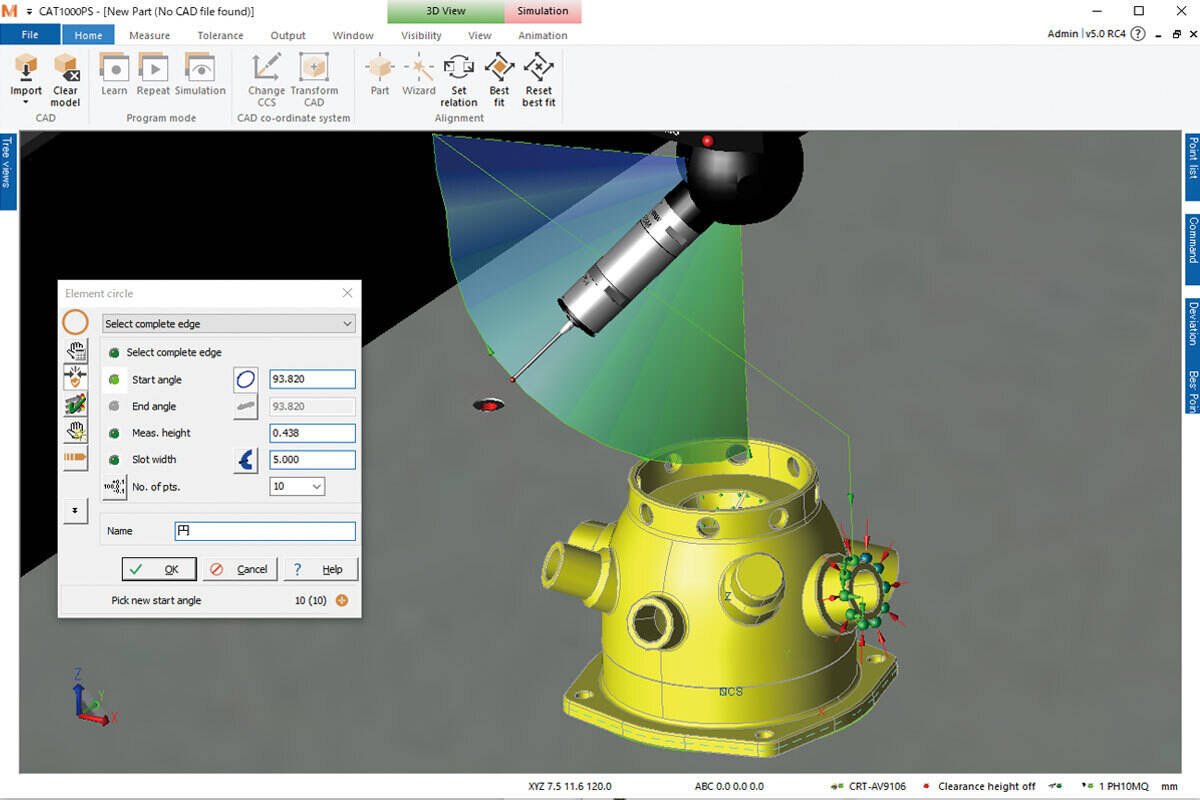
Advances In Model-based Measurement Can Reduce CMM Programming Time
With more man-hours being spent on programming work, differences in worker-created measurement programs, and inefficient programs being created due to proficiency issues, the industry has moved from 2-D drawings to 3-D annotated models. A number of factors—the increased emphasis on quality control, the growing diversity of parts and components being measured, the development of more complex global supply chains and reduced product lifecycles—have led to a considerable demand for automatic measurement programming in recent years.